Stochastic Supply Chain Planning for Lower Inventory and Accurate Commit Dates
Given the increasing nature of uncertainty in supplies and disruptions, it would be imprudent to assume a constant and pre-defined value for certain key parameters in supply chain that are in reality probabilistic in nature. Examples are supplier delivery times, equipment availability, cycle times to complete orders, reliability of transportation times, processing times or variability of supply availability. Stochastic, or non-deterministic, planning means taking into account variability on the supply side in addition to demand side. In demand planning we use probabilistic and ML methods to determine the variability of demand quantities. There is also a need to do the same on the supply side. For example, there may only be 60% probability that the vendor will deliver a shipment 21 days after the purchase order is received, and a 10% probability of it being greater than 21 days and 30% lower than 14 days. Moreover, if we know that certain supplier is more likely to deliver key items sooner than later during certain times of the year, this could have a huge impact on lowering inventory and faster delivery to the customers.
The kind of data that is needed to determine the likely values of above-mentioned parameters are available in most transaction systems. Using ML techniques, we can draw conclusions on the likelihood of having the items needed at the time that is needed, whether it is material or capacity. Furthermore, it can be decided whether the suppliers and contract manufacturers are likely to deliver what is needed when a large order is received or if there is a drastic upward shift in demand. Thus, one can respond immediately to the clients with a higher degree of confidence in real-time, without even checking with the suppliers or CMs.
Creating a supply chain twin means a digital model of the physical supply chain as accurately as possible and having the ability to change as the physical world changes resulting in accuracy in planning, commit dates and financial outcomes. By taking into account the variability of said parameters, more accurate plans are produced resulting in much more accurate commit dates, lower inventory by not keeping redundant inventory while waiting for other parts to arrive and avoid expediting and the use of more expensive part numbers or transportation methods. The resulting system becomes more predictable because of its accurate representation of the true capability of the physical supply chain. Hence more resiliency and less risk and surprises.
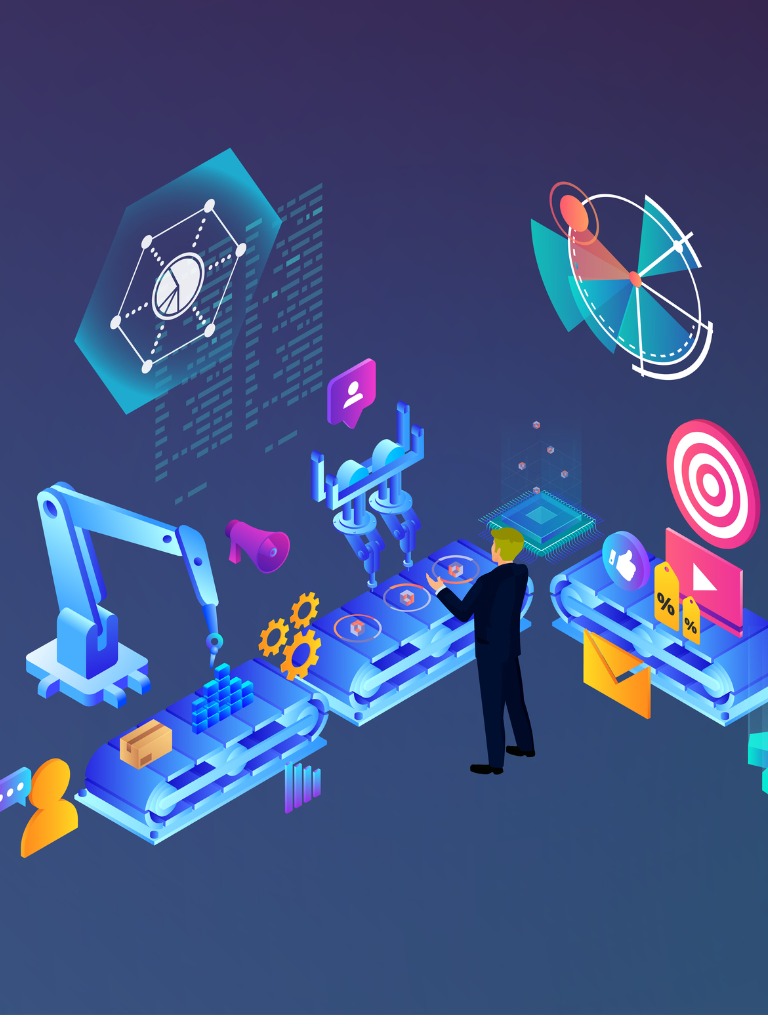