S&OP is good, but why not great!
If you are reading this, you are very familiar with S&OP solutions and their benefits. You might even be a user of S&OP and recently implemented one. Then the questions to ask are:
How accurate are your Sales and Operations Planning S&OP generated supply plans? Is it accurate enough to be executed without constant user modifications?
- Do you have the ability to truly optimize your sourcing choices or even manufacturing sites alternatives?
- Do you have order level pegging capability?
- Are you modeling the capacities in buckets just like a spreadsheet technique of the ’60s?
- Are you assuming static and fixed lead-times for your manufacturing?
- Are you defining bottleneck work centers statically rather than the system being able to identify them dynamically based on product mix?
- Does your S&OP provide a release production plan that is executable by the sites?
- Can you trace final demand orders all the way back to suppliers and their attributes?
- Can you specify alternative methods of production and sourcing based on cost and optimization?
- Do your long-term plans and short-term execution plans sync?
- Does your plan perform inventory optimization at different stages of the supply chain?
- Does the system give you accurate ATP/CTP in sub-seconds?
If you answered “NO” to any of the above then you might as well use a spreadsheet for your supply-side planning, because that is exactly what you will pay for to have an S&OP system that does not have execution capability or S&OE (Sales and Operations Execution as defined by Gartner). We firmly believe that A good plan is one that can be executed, otherwise, it is wishful thinking and a waste of time. Plan accuracy depends on the ability of the system to model your supply chain environment realistically not like a spreadsheet, volume based in buckets! To learn more about how Adexa enhances S&OP with S&OE, click Here
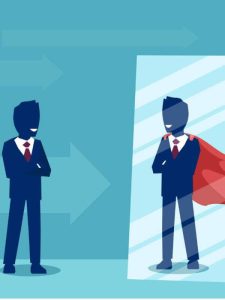