Planning & Manufacturing Execution are Inseparable
According to Gartner, “Supply chain planning has limited visibility into the ever-changing complexities (such as changeovers, rework, labor constraints, differences in understanding of resources, process differences for make-to-order, configured orders) of manufacturing operations. This leads to the creation of inaccurate finite schedules which deviate significantly from the on-site realities that manufacturing must deal with.” The real problem is that planning and manufacturing execution have been treated as two separate processes of S&OP and S&OE. And then trying to build a “bridge” between the two. In other words, creating an unnecessary problem and then try to fix it. There is really no need for separation of MPS, RCCP and factory planning & scheduling and even sequencing. These processes were designed in the 80’s when the only tool available was a spreadsheet. We can do better. Planning and execution of the plans need to be treated as a continuum. In the absence of this, we plan and throw it over the wall and then the execution throws it back at the planning process. The current approach uses a different understanding of what the real constraints are at each level. At the high level, the actual execution constraints, including capacities, availability of tools and labor, are not fully understood. At the execution level, the business constraints and objectives are not considered when disruptions occur and surprise orders arrive.
A continuum of planning and manufacturing execution removes these “vertical silos” and enables smooth planning and execution on a continuous basis. To this end, planning process and system have a good understanding of the manufacturing constraints and the impact of product mix on capacities. This yields the creation of more realistic plans resulting in smooth execution, reliable commits and enhanced financial projections. For more information on how to plan and execute as a continuum, click Here.
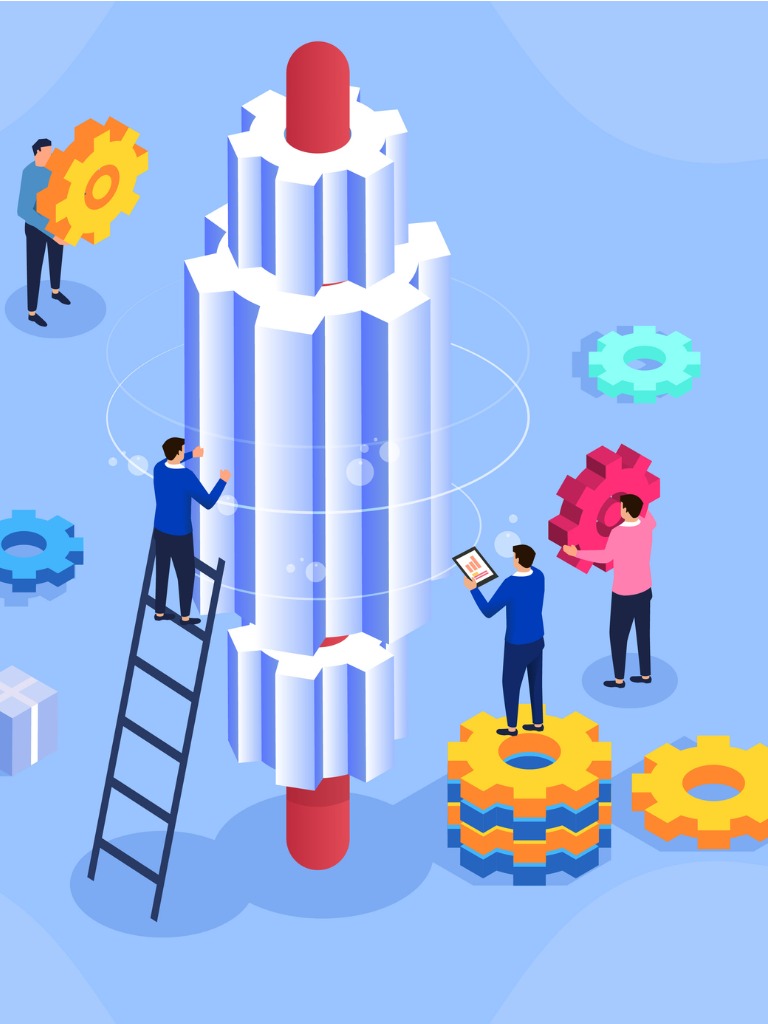