Mastering Respond Planning with Prediction
According to a recent study, supply chain disruptions are costing hundreds of millions of dollars every year. These are companies that are already doing “planning,” yet disruptions are the problem. Given the complexity of today’s supply chain, the task of planning has changed a great deal from what it used to be 30 years ago, when sales and operations planning processes were developed. Planning is no longer just about customer demand but also international regulations, resilience, agility, environmental factors & sustainability, transparency, and above all ability to predict and respond in real-time. Not just “plan now and respond later.” Unfortunately, today’s practice with most technology providers is plan now and somebody else will take care of all the issues, predictable or not, later. With S&OP, we integrate supply chains horizontally, why not do the same vertically? That is, planning and execution in one.
Most real issues occur because of a lack of better understanding of the supply chain and the ability to capture that in a digital model, aka a supply chain digital twin. If you have a bird’s eye view of the supply chain which is what S&OP solutions are, how would it be possible to account for potential issues happening or expected to happen at the street level? However, no matter how good the plan and how good the digital model is, there are still unexpected issues or disruptions. A plan may give you some visibility, so what? A manual approach of trying to understand the behavior of the supply chain, suppliers, customers, availability of resources, cost and profitability factors etc., is at best sub-optimal and maybe just good enough. “Good enough” is not what most leaders go for. The ability to predict and respond in real-time in such a complex and uncertain world is the key to having a resilient and agile supply chain. How else can you be agile and resilient? Now is the time to put the technology to work, not just give you visibility but provide guidance, advice, and recommendations.
Respond planning comes in two forms. If you have an adequate digital model of the supply chain and operations, then you can predict better. When you predict better, then more resilient plans are created that results in avoidance of many disruptions. Then there are events that are either not predictable or the system is incapable of predicting them. Some examples of these events are sudden strikes, truck’s arriving late, fire at a subcontractor, ships getting stuck at the port; or more impactful ones such as pandemics, earthquakes, and tariffs.
By far most disruptions are predictable using ML or statistical techniques. these include supplier delivery performance, shipping delays, availability of resources, customer orders, or even tornados, in certain seasons, and other Acts of God such as snowstorms in winter. Remember that planning may take care of some of these surprises, only if the system is intelligent enough and is equipped with an adequate digital model of the supply chain. Now what if it is a surprise? And there are many that typical S&OP solutions cannot predict because of lack of having a true digital model. This is where the system needs to have the capability to immediately perform automatic scenario analysis in order to find the most cost effective approach. To do so, it needs to understand the impact of the event. Not every disruption is significant enough to change the plan. However when it is an impactful event, such as a major resource going down, truck arriving late in the morning or quality issues, then it should be taken care of by the system examining all the alternatives and ensuring on-time delivery at the lowest possible cost. All that, in almost real-time. Not manual scenario analysis.
Intelligent systems can do this by sensing events, understanding their impact, finding a solution and also learning from it so that it can be predicted in future. Consider, for example, a sudden shortage of a key material needed for delivery to an important customer because of a surprise order. Depending on the impact on the commit dates, the system can search for substitute part numbers, or an alternative supplier, or even send a message to the current supplier if it can be expedited. Other options are re-shuffling the plan to give higher priority to one customer over another and still maintain committed due dates. Furthermore, advise users and potentially clients of changes in committed dates, if any, or simply partial delivery. Examining all these scenarios and trying to understand its financial implications in almost real-time is not humanly possible. Traditional, most current, S&OP solutions cannot do this for the reasons that were mentioned above.
The kind of disruptions that we are talking about are happening almost every day. S&OP planning can help but not enough as described in the study above. Many, perhaps the majority of companies, who have already implemented S&OP solutions are now wondering how they can do respond planning. Adding S&OE solutions is one approach. However, it will not present a true integration of planning and execution since they are two disjointed models of the world. They can pass data back and forth but cannot talk each other’s’ language or synch up in real-time causing decision latency. It is imperative that planning and execution is done in a unified environment forming a continuum of planning and execution. Thus, systems can plan, execute and learn continuously. This is what technology can offer today in contrast to the processes designed in the 80’s and spreadsheet technology of the past.
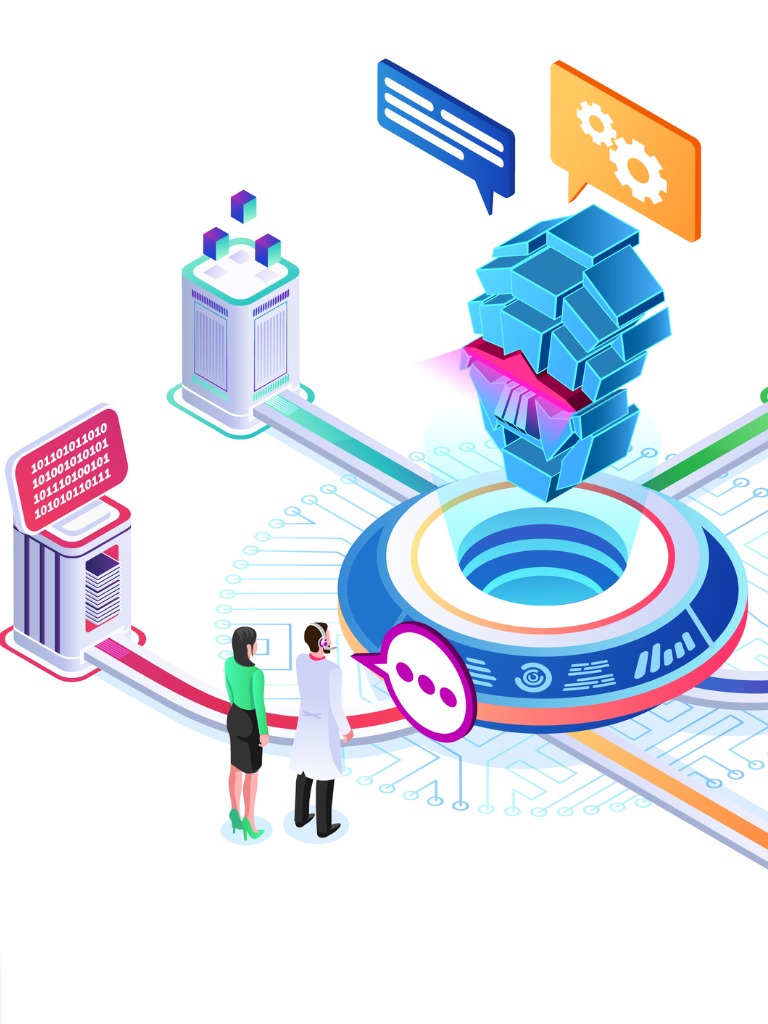